Ball bearings are complex mechanisms, with ball-to-raceway conformity, radial play and ball complement all impacting a ball bearing’s ability to support loads under various conditions. During the assembly phase, the bearing manufacturer intentionally incorporates internal looseness, or radial clearance, between the rolling elements (balls) and raceways, resulting in radial play and axial play in the bearing.
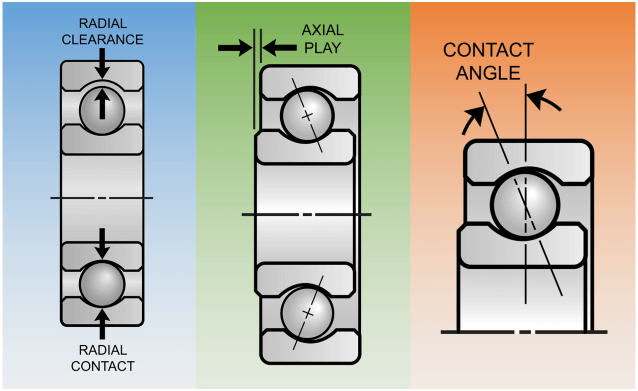
Ball complement, the number, and diameter, of balls in a bearing, is commonly known as the ball complement.
Radial play, or internal clearance, is the internal radial looseness in a bearing. It is the measured value of the total radial movement of the outer ring relative to the inner ring in a plane that is perpendicular to the bearing axis. Radial play is determined by the actual raceway diameters and ball diameter.
Gages verify radial play by subjecting the bearing to a standard gage load, ensuring full contact between all bearing components.
Axial play, or end play, is the maximum relative axial movement of the inner ring relative to the outer ring.
Both radial play and axial play are specified independently of ABEC tolerance classes for rings. Radial play is typically specified as part of the bearing part number.
In most applications using radial ball bearings, the internal looseness, or clearance, is removed by applying an axial preload across the pair of bearings, using shims, springs, take up nuts or other assembly techniques. This ensures ball to raceway contact that provides for accurate rotation and reduces or eliminates ball skidding and noise.
Contact angle in a ball bearing
A contact angle occurs when ball bearings are axially preloaded; it is the angle between a plane perpendicular to the bearing axis and a line joining the two contact points between the ball and the inner and outer raceways. Additional axial loads increase the contact angle. As radial play increases, the contact angle also increases.
General design considerations
There are numerous considerations for radial play values in a specific bearing application. Each choice impacts noise, vibration, and heat, among other factors.
Fitting
When the bearing is mounted using interference fits, allow for more radial play (the radial play after mounting is of primary importance).
Loading
When a ball bearing is subjected to pure radial loads, we recommend lower radial play, which distributes the load over more balls.
Misalignment
When there is a high degree of shaft deflection, increase radial play, which allows for greater misalignment
Temperature
When a high-temperature gradient exists between the rings (inner, outer), we recommend a looser radial play.
Speed
High values of radial play result in high values of contact angle. As rotational speed increases, gyratory forces on the balls increases, creating a sliding action between the balls and raceways. This results in lubricant film failure increased heat and potentially premature failure. The magnitude of the gyratory moment is related to the contact angle. The balance between the benefits of contact angle reducing stress must be weighed against the potential for lubricant failure due to ball slippage.
For more information, read, “Radial Play and Internal Clearance in Ball Bearings,” written by AST Bearings engineers.
Let our team of experts help with your bearing needs. Contact them here or learn more about our custom solutions.
Additional resources and information
- AST Bearings is proudly presenting our new certificates for both the NJ and CA locations: AST Bearings’ ISO 9001:2015 Certificates
- To learn more about ISO 9001 standard and how AST verifies customer satisfaction: Learn About AST Bearings’ certification to ISO 9001:2015