1 Ball Bearing, 7 Pieces, 2 Billion Varieties
The following is a copyrighted article which first appeared in the magazine entitled, "GRW Rotation" in Volume 1/2011 in July 2011 and is reprinted with permission.
At first glance the design of a ball bearing is clear: An inner ring is mounted with an outer ring, the appropriate balls and retainer. Then the ball bearing is combined with the lubricant adapted to the requirements of use and if necessary a shield to protect against contamination.
Due to the numerous norms and installation recommendations in the area of the rolling bearing the external dimensions of the various ball bearing manufacturers only differ in nuances. The big differences become obvious in the internal values of the ball bearing, the materials used for rings and retainers, number of balls and their diameter, surface structure and profile precision, as well as the lubricant used.
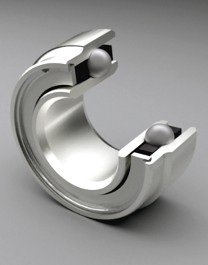
GRW has according to requirements three different materials to choose from for the ball bearing rings. You can choose between 100Cr6, X65Cr13 (SS), or X35CrMoN15-1 (SV30). Regardless of whether the customer‘s focus is on hardness, operating temperature or corrosion resistance, in the hardening process developed by GRW the desired properties can be specifically called up and implemented in the in house hardening shop. In order to obtain further functional properties from the bearing ring, it can additionally be provided with coatings.
For a long time GRW has invested significant development effort in the coating of ball bearings. The aim of this development is amongst other things to improve the tribological behavior or increase the corrosion resistance. Whether as a dry lubricant to increase the dry running properties or for use in high vacuum, GRW offers the best solution for every requirement, with now over 90 different coating varieties. The newest development in this area is a metal - plastic hybrid band (patent: EP000001832765B1). Hereby a metal band is coated with a thin, solid PTFE sheet and then formed into a steel ribbon retainer. Due to the low friction coefficients of PTFE, ball bearings with the lowest friction moments and an excellent life span in dry operation can be realized with this retainer coating.
Furthermore the newest procedures via PVD (Physical Vapor Deposition) or CVD (Chemical Vapor Deposition) are used and fulfill the highest standards for the coating quality. An unwanted dissolution of the coating will result in a serious early failure of the bearing. Therefore all coating varieties are subject to the strict GRW quality norms and tests.
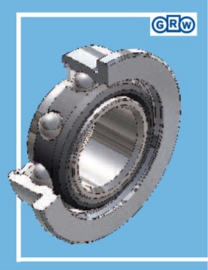
The retainer must hold the balls at an equal distance from each other and prevent them touching each other. Furthermore the retainer must have an appropriate design with defined material strengths and balanced elasticity, in order to endure the load in the ball bearing as best possible.
Apart from the tight tolerance specifications for GRW ball bearing rings regarding surface finish, form precision and steel purity, the same requirements apply to the design and production of the retainer. There are 3 basic variants for the retainers: Inner ring, outer ring or ball controlled retainer. These basic types can be combined with 21 different materials. The selection of materials covers the whole range from metal ribbon for steel ribbon retainers to special materials for aviation and space flight right up to chemically coupled heavy duty plastic “PAI - PTFE-cg” for applications with the highest standards for wear behavior, temperature resistance and sterilization ability.
Lubricants serve to reduce friction and wear, as well as cooling, shock absorption, seal effect and corrosion protection. Lubrication can be carried out using greases or oils and/or in special cases solid lubricants. All 3 types are recovered in the products of GRW. The installation situation of the ball bearing is crucial for the selection of a suitable lubricant. Grease lubrication is recommended for general use for low to medium speeds and is therefore the most frequently used lubrication type. The main part of lubricating grease consists of base oil and the smaller part consists of the appropriate thickener. Bearing lubrication is mostly carried out using base oil, which releases the thickener in small quantities over time. At GRW lime soaps, natron soaps, lithium soaps and complex soap greases are used.
Oil lubrication is used if grease lubrication cannot be used for technical or economic reasons. This can be the case with high operating temperatures, caused by ambient temperature or frictional heat in the ball bearing. Oils are divided into mineral and synthetic oils. Animal or plant oils are not suitable or only suitable to a limited extent for use in ball bearings. In total at GRW more than 400 lubricants are used and therefore cover a large area of use, from the food industry to aviation and space flight.
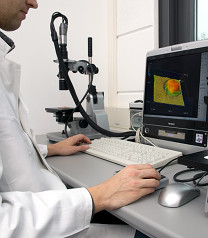
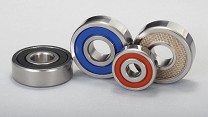
Finally the shield is mounted on the ball bearing as the last component. This should keep impurities away from the high precision functional surfaces of the bearing and therefore produce the least possible friction. On the other hand this should keep the lubricant in the bearing. Impurities which get between the ball and the raceway will be rolled over and thereby damage the processed raceways. In order to prevent this, non-contact shields and contact shields are offered, with various sealing qualities.
With the non-contact shields no increase in torque occurs, as the shield creates a gap ring. It does not produce any friction and can therefore be used even at the highest speeds.
With the contact shield the so called ball bearing seal touches the shoulder of the inner ring with a defined contact pressure and therefore causes an increased friction moment. Compared to the non-contact shields, all contact shields will wear over time. Dust shields are primarily produced from stainless steel or steel sheet reinforced Perbunan rubber. Established seals are made of a glass fiber reinforced Teflon disk or steel sheet reinforced synthetic fluorine rubber. In total there are 63 shield variants to choose from.
At GRW individual products are made from these components for the special customer requirements. Due to a sensible combination strategy from standard and special components it is possible for GRW to serve the most diverse market requirements and ensure our customers a competitive advantage.
Extensive, competent advice and design of a ball bearing are the prerequisites for the highest fulfillment of the requirements set. Even in the development phase of new applications, GRW engineers can contribute valuable technical and mostly also cost saving information.
By Alexander Strobl - GRW (Gebr. Reinfurt GmbH & Co. KG)