A long-time customer of ours that manufactures roller assemblies for use in machines that spin yarn came to us with a problem. The end user’s — those who used the roller assemblies in their yarn spinning machines — were facing disruptions. Tiny fibers were contaminating the standard catalog bearings used in the roller assemblies (those produced by our customer), which were then failing, costing their customers both time and money.
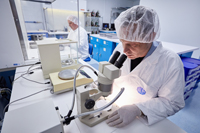
This in turn also cost our customer both time and money, as they provided a two-year warranty on their roller assemblies, since many of the bearing failures were occurring well before the warranty period had lapsed.
A typical roller has urethane over molded on an aluminum sleeve with a bearing pocket on each end, or side. The bearings are typically mounted using a light press fit. These rollers guide and move strands of yarn as they are twisted together and spooled. While the loads are extremely light, the surface speed of the fiber like strands of material passing over the urethane generates fine particulate debris that gets airborne and then settles on the machine surfaces. Most large plants operate dozens of machines and operate 24/7. Eventually, dried debris and tiny fibers find their way into the bearing resulting in premature failure.
When the failed bearing seizes, the roller abruptly stops spinning, the yarn snaps, and the whole machine must be shut down until the roller is replaced. Keep in mind, one spinning machine can contain as many as 600 roller assemblies (or 1200 bearings), and failure of a single unit could take the entire machine off-line.
Our customer simply could not tolerate any significant cost increases so making major design changes was not an option. We had to address the bearings specifically.
Contamination is a very common failure mode in bearings. In the environment described above, the normal approach would be to switch to sealed bearing. However, with such a light, sensitive load running continuously across their surface, the roller assembly needed to be “free” spinning. As such, we couldn’t add a contact style seal as it would add too much torque to the roller. In addition, with as many as 600 rollers in a machine, system torque and power became an issue.
After significant trial-and-error, our engineers arrived at an innovative solution: We added a small, thin metal washer to the face of the inner ring on each side of the bearing. The arrangement served as a barrier thus preventing fibers from entering and accumulating thru the shield gap, while maintaining the low torque characteristics of shielded bearing.
Our customer tested the modification for an entire year, eventually approving the new setup. It has proved exceptionally durable while drastically reducing disruptions for the end user’s spinning machines (running at 90% to 95% uptime), allowing our customer to successfully meet his two-year product warranty.
Our customer was able to achieve these performance gains at minimal supplemental cost, as the metal shield was relatively inexpensive. In fact, we developed a unique and proprietary process and were able to do all of the requisite work in-house, leveraging our build and test capabilities.
While sealing problems are common in the manufacture of fabrics, papers and other textiles where fine particles and fibers can enter the bearing space, finding an innovative solution is one of our core competencies and a strength that distinguishes AST in the bearing industry.
What’s your problem? Let our team of experts help with your specific needs. Contact them here or learn more about our custom solutions.